Steam engine
2007 Schools Wikipedia Selection. Related subjects: Engineering
- The term steam engine may also refer to an entire railroad steam locomotive.
A steam engine is an external combustion heat engine that makes use of the thermal energy that exists in steam, converting it to mechanical work.
Steam engines were used as the prime mover in pumps, locomotives, steam ships, traction engines, steam lorries and other road vehicles, and were essential to the Industrial Revolution. Steam turbines, technically a type of steam engine, are still widely used for generating electricity, but older types have been almost entirely replaced by internal combustion engines and electric motors.
A steam engine requires a boiler to boil water to produce steam. The expansion—or contraction—of steam exerts force upon a piston or turbine blade, whose motion can be harnessed for the work of turning wheels or driving other machinery. One of the advantages of the steam engine is that any heat source can be used to raise steam in the boiler; but the most common is a fire fueled by wood, coal or oil or the utilisation of the heat energy generated in a nuclear reactor.
Invention and development
The first recorded steam device, the aeolipile, was invented by Hero of Alexandria, a Greek, in the 1st century AD, but used only as a toy. In 1663, Edward Somerset, 2nd Marquess of Worcester published designs for, and may have installed, a steam-powered engine for pumping water at Vauxhall House.
In about 1680 the French physicist Denis Papin, with the help of Gottfried Leibniz, built a steam digester for softening bones, i.e. he invented the world's first-ever pressure cooker. Later designs implemented a steam-release valve to keep the device from exploding. By watching the valve rhythmically move up and down Papin conceived of the idea of a piston and cylinder engine. Papin wrote up the designs for such a device (as pictured adjacent), however he never built an actual steam engine. The English engineer Thomas Savery later used Papin's designs to build the world's first operational steam engine.
Papin also designed a paddle boat and is also credited with a number of significant devices such as the safety valve. Sir Samuel Morland also developed ideas for a steam engine during the same period and built a number of steam-engine pumps for King Louis XIV of France in the 1680s.
Early industrial steam engines were designed by Thomas Savery (the "fire-engine", 1698) but it was Thomas Newcomen and his "atmospheric-engine" of 1712 that demonstrated the first operational and practical industrial engine. Together, Newcomen and Savery developed a beam engine that worked on the atmospheric, or vacuum, principle. The first industrial applications of the vacuum engines were in the pumping of water from deep mineshafts. In mineshaft pumps the reciprocating beam was connected to an operating rod that descended the shaft to a pump chamber. The oscillations of the operating rod are transferred to a pump piston that moves the water, through check valves, to the top of the shaft. Early Newcomen engines operated so slowly that the valves were manually opened and closed by an attendant. An improvement was the replacement of manual operation of the valves with an operation derived from the motion of the engine itself, by lengths of rope known as potter cord (Legend has it that this was first done in 1713 by a boy, Humphrey Potter, charged with opening the valves; when he grew bored and wanted to play with the other children he set up ropes to automate the process.)
Humphrey Gainsborough produced a model condensing steam engine in the 1760s, which he showed to Richard Lovell Edgeworth, a member of the Lunar Society. In 1769 James Watt, another member of the Lunar Society, patented the first significant improvements to the Newcomen type vacuum engine that made it much more fuel efficient. Watt's leap was to separate the condensing phase of the vacuum engine into a separate chamber, while keeping the piston and cylinder at the temperature of the steam. Gainsborough believed that Watt had used his ideas for the invention, but there is no proof of this.
Watt, together with his business partner Matthew Boulton, developed these patents into the Watt steam engine in Birmingham, England. The increased efficiency of the Watt engine finally led to the general acceptance and use of steam power in industry. Additionally, unlike the Newcomen engine, the Watt engine operated smoothly enough to be connected to a drive shaft—via sun and planet gears—to provide rotary power. In early steam engines the piston is usually connected to a balanced beam, rather than directly to a connecting rod, and these engines are therefore known as beam engines.
The next improvement in efficiency came with the American Oliver Evans and the Briton Richard Trevithick's use of high pressure steam. Trevithick built successful industrial high pressure single-acting engines known as Cornish engines. However with increased pressure came much danger as engines and boilers were now likely to fail mechanically by a violent outwards explosion, and there were many early disasters. The most important refinement to the high pressure engine at this point was the safety valve, which releases excess pressure. Reliable and safe operation came only with a great deal of experience and codification of construction, operating, and maintenance procedures.
Nicolas-Joseph Cugnot demonstrated the first functional self-propelled steam vehicle, his "fardier" (steam wagon), in 1769. Arguably, this was the first automobile. While not generally successful as a transportation device, the self-propelled steam tractor proved very useful as a self mobile power source to drive other farm machinery such as grain threshers or hay balers. In 1802 William Symington built the "first practical steamboat", and in 1807 Robert Fulton used the Watt steam engine to power the first commercially successful steamboat. On February 21, 1804 at the Penydarren ironworks at Merthyr Tydfil in South Wales, the first self-propelled railway steam engine or steam locomotive, built by Richard Trevithick, was demonstrated.
Reciprocating engines
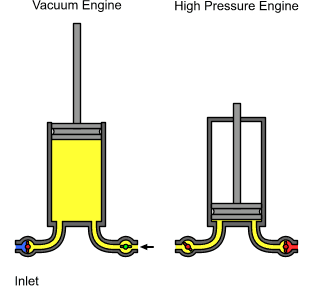
Reciprocating engines use the action of steam to move a piston in a sealed chamber. The reciprocal action of the piston can be translated via a mechanical linkage into rotary work.
Vacuum engines
Early steam engines, such as Newcomen's "atmospheric" and Watt's "condensing" engines, worked on the vacuum principle and are thus known as vacuum engines. Such engines operate by admitting low pressure steam into an operating chamber and closing the inlet valve. The steam is then cooled, the resultant water vapor condensing to a smaller volume than the steam, creating a vacuum in the chamber. Atmospheric pressure, operating on the opposite side of a piston, pushes the piston to the bottom of the chamber. The piston is connected to a large beam and counterweight, the weight of which returns the piston to the top of the chamber; the low pressure steam is insufficient to move the piston upwards alone. The reciprocating action of the beam can be harnessed to do mechanical work. In the Newcomen engine cooling water is sprayed directly into the working chamber but in the Watt engine there is a separate condensing chamber, connected to the working chamber by a valve. The inefficiency of the Newcomen engine lay in the repeated and wasteful heating and cooling of the working chamber. By removing the condensing phase of the action to a separate chamber this was greatly reduced and the efficiency of the engine was greatly increased.
Vacuum engines are severely limited in their efficiency but are relatively safe since the steam is at very low pressure and structural failure of the engine will be by inward collapse rather than an outward explosion. Their power is limited by the ambient air pressure, the displacement of the working chamber, the combustion and evaporation rates and—where present—the condenser capacity. The maximum theoretical efficiency is limited by the relatively low boiling point of water at near atmospheric pressure (100 °C, 212 °F).
High pressure engines
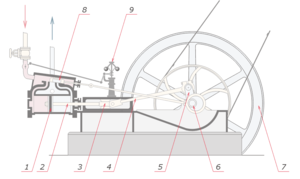
1 - Piston
2 - Piston rod
3 - Crosshead bearing
4 - Connecting rod
5 - Crank
6 - Eccentric valve motion
7 - Flywheel
8 - Sliding valve
9 - Centrifugal governor.
In a high pressure engine, steam is raised in a boiler to a high pressure and temperature. It is then admitted to a working chamber where it expands and acts upon a piston, although Trevithick's original " Cornish engines" used steam pressure alone to raise the cylinder. The piston consequently reciprocates, much like in the vacuum engine. The importance of raising steam under pressure (from a thermodynamic standpoint) is that it attains a higher temperature. Thus, any engine using such steam operates at a higher temperature differential than is possible with a low pressure vacuum engine. After displacing the vacuum engine, the high pressure engine became the basis for further development of reciprocating steam technology. High pressure steam also has the advantage that engines can be much more compact. The significance is that engines could be developed that were small enough and powerful enough to propel themselves while doing useful work; steam power for transportation became a practicality.
Double-acting pistons
The next major advance in high pressure steam engines was the use of double-acting pistons. In the simple-acting high pressure engine above, the cylinder is vertical and the piston returns to the start—or bottom—of the stroke by gravity. In the double-acting piston, steam is admitted alternately to each side of the piston while the other is exhausting. This requires inlet and exhaust ports at either end of the cylinder (see the animated expansion engine below) with steam flow being controlled by valves. This system increases the speed and smoothness of the reciprocation and allows the cylinder to be mounted horizontally or at an angle. Power is transmitted from the piston by a sliding rod—sealed to the cylinder to prevent the escape of steam—which in turn drives a connecting rod via a sliding crosshead bearing). This converts the reciprocating motion to a rotary motion. The inlet and exhaust valves have a motion derived from the rotary motion by way of an additional crank mounted eccentrically (i.e off centre) from the drive shaft. The valve gear may include a reversing mechanism to allow reversal of the rotary motion.
Most reciprocating engines now use this technology, notable examples including steam locomotives and marine triple expansion engines. When a pair (or more) of double acting cylinders, for instance in a steam locomotive, are connected to a common driveshaft their crank phasing is offset by an angle of 90 degrees. This is called quartering and ensures that the engine will always operate, no matter what position the crank is in. Some engines have used only a single double-acting piston, driving paddlewheels on each side by connection to an overhead rocker arm. When shutting down such an engine it was important that the piston be away from either extreme range of its travel so that it could be readily restarted (as there is not a second quartered piston to prevent this).
Compounding
1 - High pressure cylinder
2 - High pressure crank
3 - Flywheel
4 - Low pressure crank ("quartered")
5 - Low pressure cylinder.
1 - Low pressure cylinder
2 - High pressure cylinder
3 - Connecting rod
4 - Driveshaft & flywheel.
All of the high pressure engines mentioned above use simple expansion—the steam enters the cylinder, expands once and exhausts. As steam expands its temperature drops, this is known as adiabatic expansion. This results in steam entering the cylinder at high temperature and leaving at low temperature. This causes a cycle of heating and cooling of the cylinder with every stroke which is a source of inefficiency.
A method to lessen the magnitude of this heating and cooling was invented in 1804 by British engineer Arthur Woolf, who patented his Woolf high pressure compound engine in 1805. In the compound engine, high pressure steam from the boiler expands in a high pressure cylinder and then enters one or more subsequent lower pressure cylinders. The complete expansion of the steam now occurs across multiple cylinders and as less expansion now occurs in each cylinder so less heat is lost by the steam in each. This reduces the magnitude of cylinder heating and cooling, increasing the efficiency of the engine. To derive equal work from lower pressure steam requires a larger cylinder volume as this steam occupies a greater volume. Therefore the bore, and often the stroke, are increased in low pressure cylinders resulting in larger cylinders. Where space is at a premium, such as in a steam locomotive, two cylinders of a smaller volume are often substituted.
The first compound engines had 2 cylinders, often called double compound, with later types of compound engines using triple and even quadruple expansion (see below). The difference between the inlet and exhaust temperature of the steam in each cylinder in a double compound is roughly half that in a simple expansion engine, with the pistons designed so that each produces half the work of the engine.
The arrangement of cylinders in double compound engines are used as a basis for classification:
- Cross compound - The cylinders are side by side and drive the same crank.
- Tandem compound - The cylinders are end to end, driving a common connecting rod
- Steeple engine - A vertical tandem compound engine.
- Angle compound - The cylinders are arranged in a vee and drive a common crank.
In cross and angle compounds, the pistons are connected to the crank 90° out of phase with each other (quartered) to derive a smooth motion that will not lock up, with a new power stroke every quarter turn.
The compound engine increases the efficiency of steam engines but adds a great deal of complexity to the system. Its adoption was almost universal in industrial and marine engines, but was not so marked in railway locomotives. This is partly due to the harsh railway operating environment and limited space afforded by the loading gauge (particularly in Britain, where compounding was not common). Locomotive compounding most commonly drove two different sets of driving wheels, to better distribute the power of the engine and lessen the effects of hammer blow peculiar to steam locomotives. Most compound steam locomotives had a simpling valve that fed high pressure steam to all cylinders to help start a heavy train.
Multiple expansion
It is a logical extension of the compound engine above to split the expansion into yet more stages to increase efficiency. The result is the multiple expansion engine. Such engines use either three or four expansion stages and are known as triple and quadruple expansion engines respectively. These engines use a series of double-acting cylinders of progressively increasing diameter and/or stroke and hence volume. These cylinders are designed to divide the work into three or four, as appropriate, equal portions for each expansion stage. As with the double compound engine, where space is at a premium, two smaller cylinders of a large sum volume may be used for the low pressure stage. Multiple expansion engines typically had the cylinders arranged inline, but various other formations were used.
The images to the right show a model and an animation of a triple expansion engine. The steam travels through the engine from left to right. The valve chest for each of the cylinders is to the left of the corresponding cylinder.
The development of this type of engine was important for its use in steamships as by exhausting to a condenser the water can be reclaimed to feed the boiler, which is unable to use seawater. Land-based steam engines could exhaust much of their steam, as feed water was usually readily available. Prior to and during World War II, the expansion engine dominated marine applications where high vessel speed was not essential. It was however superseded by the steam turbine where speed was required, for instance in warships and ocean liners. HMS Dreadnought of 1905 was the first major warship to replace the proven technology of the reciprocating engine with the then novel steam turbine.
Uniflow Engines
Another type of steam engine is the uniflow type, the name deriving from the fact that steam flowed in one direction only in each half of the cylinder. Thermal efficiency was increased in the compound and multiple expansion types by separating expansion into steps in separate cylinders. In the uniflow design, thermal efficiency is achieved by having a temperature gradient along the cylinder. Steam always enters at the hot ends of the cylinder and exhausts through ports at the cooler centre. By this means the relative heating and cooling of the cylinder walls is reduced.
Steam entry is usually controlled by poppet valves (which act similarly to those used in internal combustion engines) that are operated by a camshaft. The inlet valves open to admit steam when minimum expansion volume has been reached at the start of the stroke. For a period of the crank cycle steam is admitted and the poppet inlet is then closed, allowing continued expansion of the steam during the stroke, driving the piston. Near the end of the stroke the piston will expose a ring of exhaust ports mounted radially around the centre of the cylinder. These ports are connected by a manifold and piping to the condenser, lowering the pressure in the chamber to below that of the atmosphere causing rapid exhausting. Continued rotation of the crank moves the piston. From the animation the features of a uniflow engine can be seen, with a large piston almost half the length of the cylinder, poppet inlet valves at either end, a camshaft (whose motion is derived from that of the driveshaft) and a central ring of exhaust ports.
The beauty of the uniflow engine was that it potentially allowed great expansion in a single cylinder without the relatively cool exhaust steam flowing across the hot end of the working cylinder and steam ports of a conventional "counterflow" steam engine during the exhaust stroke. This condition allows high thermal efficiency. The exhaust ports were only open for a short period of the stroke, therefore not all expanded steam was able to exhaust. This remaining steam was compressed by the returning piston and was thermodynamically desirable as it preheated the hot end of the cylinder before the admission of steam. However, the risk of excessive compression often resulted in small auxiliary exhaust ports being included at the cylinder heads. Such a design may be called a semi-uniflow engine.
In practice the uniflow engine has a number of operational shortcomings. The large expansion ratio requires a large cylinder volume. To gain the maximum potential work from this a high reciprocation rate was required, typically 80% faster than a double-acting engine. This caused the opening times of the inlet valves to be very short, putting great strain on a delicate mechanical part. In order to withstand the huge mechanical forces encountered, engines had to be heavily built and a large flywheel was required to smooth out the variations in torque as the steam pressure rapidly rose and fell in the cylinder. Additionally, as there was a thermal gradient across the cylinder, the metal of the wall expanded to different extents. This required precise boring of the cylinder barrel to be wider in the cool centre than at the hot ends. If the cylinder was not heated correctly, or if water entered, the delicate balance could be upset causing seizure mid-stroke or, potentially, destruction.
Engines of this type usually have multiple cylinders in an inline arrangement and may be single or double acting. A particular advantage of this type is that the valves may be operated by the effect of multiple camshafts, and by changing the relative phase of these camshafts, the amount of steam admitted may be increased for high torque at low speed and may be decreased at cruising speed for economy of operation, and by changing the absolute phase the engine's direction of rotation may be changed. The uniflow design also maintains a constant temperature gradient through the cylinder, avoiding passing hot and cold steam through the same end of the cylinder.
The uniflow engine was first used in Britain in 1827 by Jacob Perkins and was patented in 1885 by Leaonard Jennett Todd. It was popularised by German engineer Johann Stumpf in 1909, with the first commercial stationary engine produced a year previously in 1908.
The uniflow principle was mainly used for in industrial power generation, but was also tried in a few railway locomotives in England, such as The NER Uniflow Locomotive No 825 of 1913, The NER Uniflow Locomotive No 2212 of 1919, and The Midland Railway Paget locomotive. Experiments were also made in the USA and Russia. In no case were the results encouraging enough for further development to be undertaken.
The final commercial evolution of the Uniflow engine occurred in the USA during the late 1930s and 1940s by the Skinner Engine Company with the development of the Compound Unaflow Marine Steam Engine. This engine operated in a steeple compound configuration and provided efficiencies approaching contemporary diesels. Many bulk carriers and ferries on the Great Lakes were so equipped, several of which are still operating.
In small sizes (less than about 1000 horsepower ), reciprocating steam engines are much more efficient than steam turbines. The Whitecliffs solar steam power plant uses a three cylinder uniflow engine to generate about 25 kW electric output.
Turbine engines
A steam turbine consists of an alternating series of rotating discs mounted on a drive shaft, rotors, and static discs fixed to the turbine casing, stators. The rotors have a propellor-like arrangement of blades at the outer edge. Steam acts upon these blades, producing rotary motion. The stator consists of a similar, but fixed, series of blades that serve to redirect the steam flow onto the next rotor stage. A steam turbine exhausts into a condenser that provides a vacuum. The stages of a steam turbine are typically arranged to extract the maximum potential work from a specific velocity and pressure of steam, giving rise to a series of variably sized high and low pressure stages. Turbines rotate at very high speed, therefore are usually connected to reduction gearing to drive another mechanism, such as a ship's propeller, at a lower speed. A turbine rotor is also capable of providing power when rotating in one direction only. Therefore a reversing stage or gearbox is usually required where power is required in the opposite direction.
The main use for steam turbines is in electricity generation (about 86% of the world's electric production is by use of steam turbines)and to a lesser extent as marine prime movers. In the former, the high speed of rotation is an advantage, and in both cases the relative bulk is not a disadvantage. Virtually all nuclear power plants and some nuclear submarines, generate electricity by heating water to provide steam that drives a turbine connected to an electrical generator for main propulsion. A limited number of steam turbine railroad locomotives were manufactured . While they met with some success for long haul freight operations in Sweden and elsewhere, steam turbines were not ideally suited to the railroad environment. Turbine locomotives did not persist in the railway world and were replaced by diesel locomotives.
Steam turbines provide direct rotational force and therefore do not require a linkage mechanism to convert reciprocating to rotary motion. Thus, they produce smoother rotational forces on the output shaft. This contributes to a lower maintenance requirement and less wear on the machinery they power than a comparable reciprocating engine.
Other engines
Other types of steam engine have been produced and proposed, but have not been nearly so widely adopted as reciprocating or turbine engines.
Rotary steam engines
It is possible to use a mechanism based on a pistonless rotary engine such as the Wankel engine in place of the cylinders and valve gear of a conventional reciprocating steam engine. Many such engines have been designed, from the time of James Watt to the present day, but relatively few were actually built and even fewer went into quantity production; see link at bottom of article for more details. The major problem is the difficulty of sealing the rotors to make them steam-tight in the face of wear and thermal expansion; the resulting leakage made them very inefficient. Lack of expansive working, or any means of control of the cutoff is also a serious problem with many such designs. By the 1840's it was clear that the concept had inherent problems and rotary engines were treated with some derision in the technical press. However, the arrival of electricity on the scene, and the obvious advantages of driving a dynamo directly from a high-speed engine, led to something of a revival in interest in the 1880s and 1890s, and a few designs had some limited success.
Of the few designs that were manufactured in quantity, those of the Hult Brothers Rotary Steam Engine Company of Stockholm, Sweden, and the spherical engine of Beauchamp Tower are notable. Tower's engines were used by the Great Eastern Railway to drive lighting dynamos on their locomotives, and by the Admiralty for driving dynamos on board the ships of the Royal Navy. They were eventually replaced in these niche applications by steam turbines.
Jet type
Invented by Australian engineer Alan Burns and developed in Britain by engineers at Pursuit Dynamics, this underwater jet engine uses high pressure steam to draw in water through an intake at the front and expel it at high speed through the rear. When steam condenses in water, a shock wave is created and is focused by the chamber to blast water out of the back. To improve the engine's efficiency, the engine draws in air through a vent ahead of the steam jet, which creates air bubbles and changes the way the steam mixes with the water.
Unlike in conventional steam engines, there are no moving parts to wear out, and the exhaust water is only several degrees warmer in tests. The engine can also serve as pump and mixer. This type of system is referred to as 'PDX Technology' by Pursuit Dynamics.
Rocket type
The aeolipile represents the use of steam by the reaction principle, although not for direct propulsion.
In more modern times there has been limited use of steam for rocketry—particularly for rocket cars. The technique is simple in concept, simply fill a pressure vessel with hot water at high pressure, and open a valve leading to a suitable nozzle. The drop in pressure immediately boils some of the water and the steam leaves through a nozzle, giving a significant propulsive force.
It might be expected that water in the pressure vessel should be at high pressure; but in practice the pressure vessel has considerable mass, which reduces the acceleration of the vehicle. Therefore a much lower pressure is used, which permits a lighter pressure vessel, which in turn gives the highest final speed.
There are even speculative plans for interplanetary use. Although steam rockets are relatively inefficient in their use of propellant, this very well may not matter as the solar system is believed to have extremely large stores of water ice which can be used as propellant. Extracting this water and using it in interplanetary rockets requires several orders of magnitude less equipment than breaking it down to hydrogen and oxygen for conventional rocketry.
Applications
Steam engines can be classified by their application:
Stationary engines
Stationary steam engines can be classified into two main types:
- Winding engines, rolling mill engines, (marine engines) and similar applications which need to frequently stop and reverse.
- Engines providing power, which stop rarely and do not need to reverse. These include engines used in thermal power stations and those that were used in mills, factories and to power cable railways and cable tramways before the widespread use of electric power. Very low power engines are used to power model ships and speciality applications such as the steam clock.
Vehicle engines
Steam engines have been used to power a wide array of types of vehicle:
- Steamboat and steamship
- Land vehicles:
- Steam locomotive
- Steam car
- Steam lorry
- Steam roller
- Steam shovel
- Traction engine
Advantages
The strength of the steam engine for modern purposes is in its ability to convert heat from almost any source into mechanical work. Unlike the internal combustion engine, the steam engine is not particular about the source of heat. Most notably, without the use of a steam engine nuclear energy could not be harnessed for useful work, as a nuclear reactor does not directly generate either mechanical work or electrical energy—the reactor itself simply heats or boils water. It is the steam engine which converts the heat energy into useful work. Steam may also be produced without combustion of fuel, through solar concentrators. A demonstration power plant has been built using a central heat collecting tower and a large number of solar tracking mirrors, (called heliostats). (see Whitecliffs Project)
Similar advantages are found in a different type of external combustion engine, the Stirling engine, which offers efficient power in a compact engine.
Steam locomotives are especially advantageous at high elevations as they are not adversely affected by the lower atmospheric pressure. This was inadvertently discovered when steam engines operated at high altitudes in the mountains of South America were replaced by diesel-electric engines of equivalent sea level power. They were quickly replaced by much more powerful locomotives capable of producing sufficient power at high altitude.
In Switzerland (Brienz Rothhorn) and Austria (Schafberg Bahn) new rack steam locomotives have proved very successful. They were designed based on a 1930s design of Swiss Locomotive and Machine Works (SLM) but with all of today's possible improvements like roller bearings, heat insulation, light-oil firing, improved inner streamlining, one-man-driving and so on. These resulted in 60 percent lower fuel consumption per passenger and massively reduced costs for maintenance and handling. Economics now are similar or better than with most advanced diesel or electric systems. Also a steam train with similar speed and capacity is 50 percent lighter than an electric or diesel train, thus, especially on rack railways, significantly reducing wear and tear on the track. Also, a new steam engine for a paddle steam ship on Lake Geneva, the Montreux, was designed and built, being the world's first ship steam engine with an electronic remote control. The steam group of SLM in 2000 created a wholly-owned company called DLM to design modern steam engines and steam locomotives.
Efficiency
To get the efficiency of an engine, divide the number of joules of mechanical work that the engine produces by the number of joules of energy input to the engine by the burning fuel. In general, the rest of the energy is dumped into the environment as heat. No pure heat engine can be more efficient than the Carnot cycle, in which heat is moved from a high temperature reservoir to one at a low temperature, and the efficiency depends on the temperature difference. Hence, steam engines should ideally be operated at the highest steam temperature possible, and release the waste heat at the lowest temperature possible.
In practice, a steam engine exhausting the steam to atmosphere will have an efficiency (including the boiler) of 1% to 8%, but with the addition of a condenser the efficiency may be greatly improved. A power station with steam reheat, etc. will achieve 30% to 42% efficiency. Combined cycle in which the burning material is first used to drive a gas turbine can produce 50% to 60% efficiency. It is also possible to capture the waste heat using cogeneration in which the residual steam is used for heating. It is therefore possible to use about 90% of the energy produced by burning fuel—only 10% of the energy produced by the combustion of the fuel goes wasted into the atmosphere.
One source of inefficiency is that the condenser causes losses by being somewhat hotter than the outside world, although this can be mitigated by condensing the steam in a heat exchanger and using the recovered heat, for example to pre-heat the air being used in the burner of an external combustion engine.
The operation of the engine portion alone is not dependent upon steam; any pressurised gas may be used. Compressed air is sometimes used to test or demonstrate small model "steam" engines.
Festivals and museums
- Antique Gas & Steam Engine Museum - Bi-Annual show in Vista, CA, Specializing in farm equipment, engines, and machinery from 1850-1950
- Great Dorset Steam Fair - annual show in England - specialises in showing engines being used in their original context: heavy haulage, threshing, sawing, road making, etc
- Annual Steam Show in America North American Model Engineering Society (NAMES)
- Annual Steam-Up in America New England Wireless and Steam Museum
- The Newcomen Engine House, Dartmouth, Devon, England, UK
- Steam Era in Milton, Ontario
- Ontario Agricultural Museum in Milton, Ontario
- Missouri River Valley Steam Engine Association Back to the Farm Reunion in central Missouri, USA. This is not a steam-only festival, but it has always had a good showing of running steam engines.
- Hamilton Museum of Steam and Technology in Hamilton, Ontario. An old municipal pumphouse dating to 1860 with its original two Woolf Compound Rotative Beam Engines, one of which still operates.
- Kempton Park Steam Engines
- Kew Bridge Steam Museum
- Crofton Beam Engines
- Bancroft Mill Engine , Barnoldswick. Movie of engine operating here
- Buckley Old Engine Show Northwest Michigan Engine & Thresher Club. Annual show (39 years) showing steam engines and equipment, antique gas and oil engines, antique agricultural equipment, mills, blacksmithing, and foundries. Show includes steam building seminars.
- Hollycombe Steam Fair