Pottery
2007 Schools Wikipedia Selection. Related subjects: Art; Business; Everyday life
Pottery is a type of ceramic material, which the American Society for Testing and Materials (ASTM) has defined as "(a)ll fired ceramic wares that contain clay when formed, except technical, structural, and refractory products." The term pottery is also used for a technique involving ceramic, where clay is mixed with other minerals and is formed into objects, including vessels generally designed for utilitarian purposes.
A Pottery is a facility of any size, from a modest studio to an industrialized factory, where pottery is made. Where resources are available - raw materials, workers, transportation - groups of potteries may exist. Due to the large number of pottery factories, or colloquially 'Pot Banks', the City of Stoke-on-Trent in England became known as The Potteries; one of the first industrial cities of the modern era where as early as 1785 200 pottery manufacturers employed 20,000 workers. The Potters is the nickname of the local football club, Stoke City F.C.. The same name is used for sports teams in the one-time "Pottery Capital of the World," East Liverpool, Ohio.
Pottery production is a process by which a clay body, clay mixed with other minerals, is shaped and allowed to dry. The shaped clay body, or piece, ware or article, may be "bisque or biscuit fired" in a kiln to induce permanent changes that result in increased mechanical strength, and then fired a second time after adding a glaze or a piece may be once fired by applying appropriate glaze to the dry unfired body and firing in one cycle.
With mass production techniques having replaced the traditional role studio potters have focused more on the aesthetic than the utilitarian
Traditionally, different regions of the world have used produced different types of clay, sometimes mixed with other minerals, to produce regionally distinctive pottery. It is common for different clays and minerals to be mixed to produce clay bodies suited to specific purposes. Pottery that is fired at temperatures in the 800 to 1200 °C range, which does not vitrify in the kiln but remains slightly porous is often called earthenware or terra cotta. Clay bodies formulated to be fired at higher temperatures, which is partially vitrified is called stoneware. Fine earthenware with a white tin glaze is known as faience. Porcelain is a very refined, smooth, white body that, when fired to vitrification, can have translucent qualities
Techniques
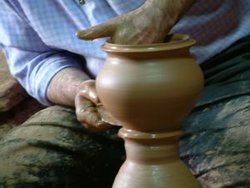
A person who makes pottery is traditionally known as a potter. The potter's most basic tool is his or her hands, however many additional tools have been created over the long history of pottery manufacture, including the potter's wheel, various paddles, shaping tools (or ribs), slab rollers, and cutting tools.
Forming techniques
Pottery can be shaped by a range techniques, including:
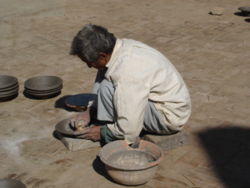
Handwork can be considered both the most primitive and the most individualized techniques, where pieces are constructed from hand-rolled coils, slabs, ropes, and balls of clay body, often joined with a slurry of clay body, known as slip. No two pieces of handwork will be exactly the same, so it is not suitable for making precisely matched sets of items such as dinnerware. Doing handwork enables the potters to use their imagination to create one-of-a-kind works of art. These methods are often referred to as "handbuilding".
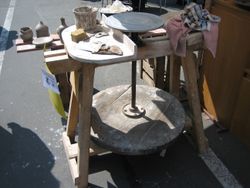
The potter's wheel. A ball of clay body is placed in the centre of a turntable, called the wheel head, which is turned either using foot power (a kick wheel or treadle wheel) or a variable speed electric motor. Oftentimes, a bat (a disk of plastic, wood, or plaster) is affixed to the wheel head, and the ball of clay body is attached to the bat rather than the wheel head so that the finished piece can be removed easily without distorting the piece. The wheel is made to revolve rapidly while the body is pressed, squeezed, and pulled gently into shape. The process of pressuring the body into a rotational symmetry, so that it does not move from side to side as the wheel head rotates is referred to as "centering" the body — a most important skill to master before the next steps, "throwing" (forming and raising the walls of the piece) and "trimming" or "turning" (removing excess clay to refine the shape or create a bottom or foot can be taken.
Potter's wheels can be used for mass production, although often it is employed to make individual pieces. Wheel work takes a lot of technical ability, but a skilled potter can produce many virtually identical plates, vases, or bowls in a day. Because of its nature, wheel work can only be used to initially create items with radial symmetry on a vertical axis. These pieces can then be altered by impressing, bulging, carving, fluting, faceting, incising, and other methods to make them more visually interesting. Often, thrown pieces are further modified by having handles, lids, feet, spouts, and other functional aspects added using the techniques of handworking. Pottery that is thrown on the wheel is often finished in a process known as trimming.
Jiggering & jolleying These can be seen to be an extension of using a Potters wheel, and in comparison allow increased speed and improved repeatability. Jiggering is the technique where a shaped tool is slowly brought down onto plastic clay body that has been placed on top of a rotating plaster mould. The jigger tool shapes one face whilst the mould the other. Jiggering is the term specific to flatware such as plates whilst a similar technique, jolleying, refers to the production of holloware like cups. These techniques have been in use since at least the 18th century Partial automation of the jiggering and jolleying processes have long been used to increased production rates and de-skill the operation
Roller-head Machine A machine for the shaping of pottery flatware on a rotating mould, as in a jigger, but with a rotary shaping tool instead of a fixed profile. The rotary tool is in the form of a shallow cone of the same diameter as the ware and shaped to produce the back of the article being made. The ware is completely shaped, by relatively unskilled labour, in one operation at a rate depending on the size of the ware of about 12 pieces per minute. The machine, developed from earlier attempts to improve on the use of a fixed tool, was patented by T. G. Green & Co. and H. J. Smith (Brit. Pat., 621 712, 14/4/49) with subsequent improvements by J. A. Johnson (Brit. Pat., 765 097, 2/1/57; 895 988, 9/5/62). It is now widely used across the world
Ram Pressing A process for the plastic shaping of tableware and sanitaryware by pressing a bat of the prepared body between two porous plates or mould units; after the pressing operation, air is blown through the porous mould parts to release the shaped ware. Although the process was patented in 1952 by Ram Incorporated, US Pats, 2 584 109 & 10, the term is often used for similar type shaping processes
Granulate pressing This involves the shaping of ware by compressing semi-dry and granulated body in a die, one side of which is a solid surface and the other a flexible membrane through which fluid pressure, of up to 100 MN.m-2, is transferred. The granulate is produced by spray drying to give a fine and free flowing material with a low moisture content of around 5-6%. Also known as dust pressing the technique is widely used in manufacture of wall and floor tiles, and increasingly of plates
Turning is similar to that used for the shaping of metal and wood articles. A blank of clay body, with low water content in a condition known as leatherhard, is mounted on a lathe whilst a cutting tool follows a profile to removes excess material and hence leave a shaped article
Slipcasting is a technique often used for mass-production, and ideally suits shapes that can not be made by other methods. Liquid clay body slip is poured into plaster moulds, the permeability of the mould drawing water from the slip to leave a layer the clay body of the internal shape of the mould. This method is almost universally used for sanitaryware, toilets and wash basins, as well being widely used for smaller pieces such as figurines which have many intricate details
Decorative and finishing techniques
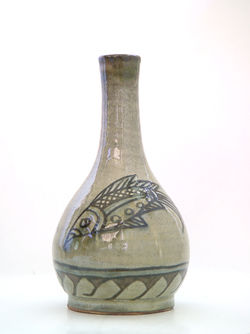
For aesthetic reasons articles can be decorated by a large variety of techniques , including the application of colours and designs. Decoration can be:
- In the body
- On the surface of the body but beneath the glaze, underglaze decoration
- In the glaze
- On the surface of the glaze, on-glaze decoration
Additives can be worked into moist clay body, prior to forming, to produce desired characteristics to the finished ware. Various coarse additives, such as sand and grog (fired clay which has been finely ground) to give the final product texture, and contrasting colored clays and grogs result in patterns. Colorants, usually metal oxides and carbonates, are added singly or in combinations to achieve a desired colour. Combustible particles can be mixed with the body or pressed into the surface to produce texture.
Agateware A long established technqiue is to partially mix different coloured clay bodies to give a distinctive 'mottled' decoration. In Great Britain, these techniques are known as agateware, after agate stone which shows similar colour banding, whilst in Japan a similar technqiue is called "neriage. An analogue of marquetry can also be made, by pressing small blocks of coloured clays together, and using the resulting mosaic to create distinctive patterns. To ensure the final articles are unfaulted, care is needed with selection to choice different bodies of compatible shrinkage and thermal expansion
Burnishing, like the metalwork technique of the same name, involves rubbing the surface of the unfired article with a suitable tool, typically of wood, steel or stone, to give a smooth, polished surface which remains even after firing. Finer clays give a smoother, shinier surface than coarser clays, as will allowing the pot to dry more before burnishing although that risks breakage
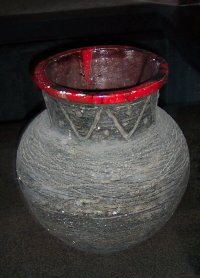
Engobe, to give a finer surface, or a coloured surface, slip can be coated onto the leather-dry body. Slip produced to a specific recipe is sometimes called an engobe. Slips or engobes can be applied by painting techniques, or the piece can be dipped for a uniform coating. Many pre-historic and historic cultures used slip as the primary decorating material on their ware. Sgraffito involves scratching through a layer of coloured slip to reveal a different colour or the base clay underneath. If done carefully, one colour of slip can be fired before a second is applied prior to the scratching or incising decoration. Often slips/engobes used in this process have a higher silica content, sometimes approaching a glaze recipe. This is particularly useful if the base clay is not of the desired colour or texture.
Banding, is the application, by hand or by machine, of a band of colour to the edge of a plate or cup. Also known as lining
Litho, is a commonly used abbreviation for lithography although alternatives names of transfer or decal or used. These are used to apply designs to artciles. The litho comprises three layers: the colour, or image, layer which comprises the decorative design; the covercoat, a clear protective layer, which may incorporate a low-melting glass; the backing paper on which the design is printed by screen printing or lithography. There are various methods of transferring the design while removing the backing-paper, some of which are suited to machine application
Gold, decoration with gold is used on some high quality ware. Different methods exist for its applications, including:
- Best gold - a suspension of gold powder in essential oils mixed with a flux and a mercury salt extended. This can be applied by a painting technique. From the kiln the decoration is dull and requires burnishing is reveal the full colour
- Acid Gold – a form of gold decoration developed in the early 1860s at Mintons Ltd., Stoke-on-Trent, UK. The glazed surface is etched with dilute hydrofluoric acid prior to application of the gold. The process demands great skill and is used for the decoration only of ware of the highest class.
- Bright Gold – consists of a solution of gold sulphoresinate together with other metal resinates and a flux. The name derives from the appearance of the decoration immediately after removal from the kiln as it requires no burnishing
- Mussel Gold – an old method of gold decoration. It was made by rubbing together gold leaf, sugar and salt, followed by washing to remove solubles
Glazing
A glaze is a vitreous coating to a ceramic material whose primary purposes include decoration or protection. Glazes can be considered specialised forms of glass. Glazing is the process of coating the piece with a thin layer of material that during firing forms the glass coating. Compositions are varied but are usually a mixture of minerals which generally, but not always, mature at temperatures lowers than the body itself. Glaze can be important for functional earthenware vessels, which would otherwise be unsuitable for holding liquids due to permeability. Glaze may be applied by dusting it over the clay, spraying, dipping, trailing or brushing on a thin slurry of glaze and water. Brushing tends not to give a very even covering but can be effective as a decorative technique. To prevent the glazed article sticking to the kiln during firing either a small part of the item is left unglazed or special refractory supports, spurs, are used as supports which are removed and discarded after the firing.
Evolution of Glazing technique
The glazing technique was greatly developed by Muslim potters who first used and improved this old tradition. In their early days (8th century), potters of Samarra and Baghdad employed lead glazes with relief designs, a technique which came down from the Romans who spread it in countries of the Mediterranean basin, including Egypt. The nature of these wares consisted mostly of red earthenware on which the shiny green or yellowish brown glazes were applied.
As they became more experienced, these potters introduced another glazing method, which they developed from attempting to imitate the popular white Chinese ceramics. In doing so, the Muslim potters introduced tin oxides to lead glaze, giving it a white finish. Lane explained how and why these potters achieved this: "It was impossible to reproduce the beautiful surface texture of these (Chinese ware) by using an ordinary clear lead glaze over a white slip, and the Mesopotamian potters therefore hit on a device used long before them by the Egyptians. Tin oxide was mixed with a modified form of lead glaze, which by the suspended particles was rendered perfectly opaque and white. When applied to a well purified yellow or pinkish clay, this glaze achieved a most deceptive similarity to the T'ang porcelain. But fortunately the Baghdad potters did not rest content as imitators. They were tempted to paint on the fine white surface, using cobalt blue, copper green, manganese purple, and sometimes antimony yellow". (Lane, A. (1947) `Early Islamic Pottery', Faber and Faber, London, p.13).
In a third stage, the Muslim potter attempted to produce a closer version of the golden and silver vessels of paradise described numerous times in the Quran. In Surah 76, for example, Allah promises His devotees: "Enter ye the Garden, ye and your wives, in (beauty and) rejoicing. To them will be passed round, dishes and goblets of gold: there will be there all that the souls could desire, all that their eyes could delight in: and ye shall abide therein (for eye). Such will be the Garden of which ye are made heirs for your (good) deeds (in life). Ye shall have therein abundance of fruit, from which ye shall have satisfaction ".(43:71-3). In Surah 43, the Exalted reminds the believers: "And amongst them (the Devotees of Allah) will be passed round vessels of silver and goblets of crystal. Crystal-clear, made of silver: they will determine the measure thereof (according to their wishes). And they will be given to drink there of a Cup (of Wine) mixed with Zanjabil, A fountain there, called Salsabil" (76:15-8). Lustre provided the right ingredients for producing such vessels in a cheaper and acceptable way as Islam prohibits the use of gold and silver vessels. This is not the first time we see Muslim craftsmen try to imitate paradise themes. Similar approach was adopted in architecture, gardening, and even carpet making. The technique involved preparing pigments by mixing silver or copper oxides with an earthy vehicle such as ochre, and then vinegar or grape juice were added as medium. This pigment is then painted onto the glassy surface of the vessel, which has been glazed and fired once. The vessel is then fired for a second time in a reducing kiln, then the ochre is rubbed away.
Firing
Firing is an essential stage in the manufacture of pottery, during which chemical and physical reactions occur which causes the material to be permanently altered. The process is carried out in a kiln.
Some clays and glazes are oxygen-sensitive, most notably those containing iron and copper, and will change colour depending on the presence of oxygen during the firing. Kilns can either be oxidized by opening a port to allow oxygen into the interior or reduced by closing off the kiln from outside air to attain colors as desired.
A number of various firing techniques can be used in addition to normal glaze-firing. Most of these involve heating the kiln to a high temperature and then delivering an amount of dry chemical into the kiln's interior. Sulphur is commonly used, as are various salts or ashes. Such substances will stick to pieces within the kiln and melt onto their surfaces, often resulting in a mottled texture which has a distinctive "orange peel" feel. Colors generally depend on what chemical is added to the kiln. These techniques can have very unusual and frequently unexpected results whether used on an unglazed piece or in combination with normal glazing.
Wood firing is another type of firing which involves using wood, rather than gas or electricity as in most modern kilns, to heat the kiln's interior. An example of a wood fired kiln is the Chinese Anagama, also adopted and used by Korean and Japanese potters. Wood firing is frequently time-consuming, as the kiln must be stoked for days, but the pieces which emerge often have characteristic patches of orange colour on the clay itself, known as "blushing".
The Western adaptation of Raku firing, a traditional Japanese technique, has enjoyed a great deal of popularity due to its relative ease. The kiln is heated to a low temperature, usually no higher than cone 06, and then ware is pulled out of the kiln while still hot (using tongs, of course) and smothered in ashes, paper, or woodchips. This can be done in an enclosed container, which allows the supply of oxygen to be cut off and reduction to take place. The finished products of this process are not suitable for functional use, as the clay remains porous and may have some toxic chemicals held within it as a result of burning the surrounding woodchips or paper used to smother it. However, because of the low temperature, it is an extremely quick and easy technique to do, and the clay has a distinctive black colour.
Production stages
All pottery items go through a series of stages during construction.
- Initially the clay body is mixed to homogenise the moisture content, and any entrapped air needs to be removed. This can be achieved either manually by a technique called wedging, or by using machines: dedicated mixers are used to homogenise the moisture whilst de-airing pugs, sometimes called pug mills, are used to remove the air. The body is then shaped either by hand or using a variety of tools and machines. Examples include the potter's wheel, extruders, rollers, jigger / jolley, RAM press and rollerhead
- Work that is thrown on the wheel often needs to be trimmed or turned to make its thickness uniform and/or to form a foot on the piece. This process is done when the piece has stiffened enough to survive manipulation. This condition is called leather hard.
- The piece is allowed to air dry until it is hard and dry to the touch. At this stage it is known as greenware. Items of greenware are very brittle but they can be handled with care. Greenware items are occasionally sanded with fine grade sandpaper to ensure a smooth finish in the completed item.
- Sometimes the greenware is given a coating of a clay slip. This is most often done to give a coloured base for decoration, other than the colour of the main body.
- The greenware is often given a preliminary firing in a kiln. Once it has been fired the articles are known as biscuit ware or bisque. Depending on historic tradition the biscuit firing can be higher or lower in temperature than the final firing
- Biscuit ware is normally a plain red, white, or brown colour depending on which type of initial raw materials used. This is decorated with glaze and then fired again to a higher temperature.
- Some pieces are not bisque-fired before being glazed. These pieces are called once-fired.
History
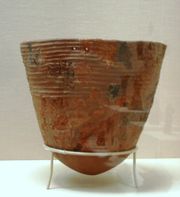
The development of pottery was a milestone in human history. These durable and watertight containers enabled people to boil and steam food which allowed them to exploit new sources of food such as shellfish, acorns, and leafy vegetables. Soft boiled foods could be eaten by toothless children and the elderly, which permitted caregivers to spend more time producing food. In Japan, for instance, the introduction of pottery was followed by a population explosion. In the archaeology of the Eastern Woodlands of North America the introduction of pottery is referred to as the container revolution.
Since pottery is a durable, man-made artifact which was utilized by various cultures around the world, it has proven to be a boon for archaeologists. Broken pottery in archaeological sites, called sherds or shards, help identify the resident culture and date the stratum by the formation, style and decoration. The relative chronologies based on pottery are essential for dating the remains of non-literate cultures and help in the dating of some historic cultures as well. Trace element analysis, mostly by neutron activation, allows the sources of clay to be accurately identified.
While ceramics had been developed in Europe also, pottery was first developed by the Jomon in Japan around 10,500 BCE. It appears that pottery was then independently developed in North Africa during the 10th millennium b.p. and in South America during the 7th millennium b.p.
The invention of the potter's wheel in Mesopotamia sometime between 6,000 and 2,400 BCE revolutionized pottery production. Specialized potters were then able to meet the burgeoning needs of the world's first cities.
While artistic value of Classical Greek and Roman pottery largely consisted of the surface decoration, the pottery itself was an important art form in China, where efficient kilns allowed high temperature ware to be fired with wood, long before the use of coal.